Pressure, an invisible and intangible physical quantity, is ubiquitous in our daily lives and industrial production. From inflating tires to probing the deep sea, the accuracy of pressure measurement is crucial, not only for product quality, but also for ensuring production safety.
In this context.The concepts of gauge pressure and absolute pressure have become the two basic types of pressure in industrial measurement. The presentThe article will take you on an in-depth exploration of these two concepts and extend them to the important application of hermeticity testing to help you understand their importance in modern manufacturing.
I. Basic concepts of pressure
1. Definition of pressure
In physics, pressure is the vertical force per unit area. In manufacturing, pressure not only affects the shape and structure of an object, but is also directly related to the stability and safety of a process. This seemingly simple definition is rich in application possibilities. From supporting skyscrapers to designing efficient airplane wings, the concept of pressure is everywhere.
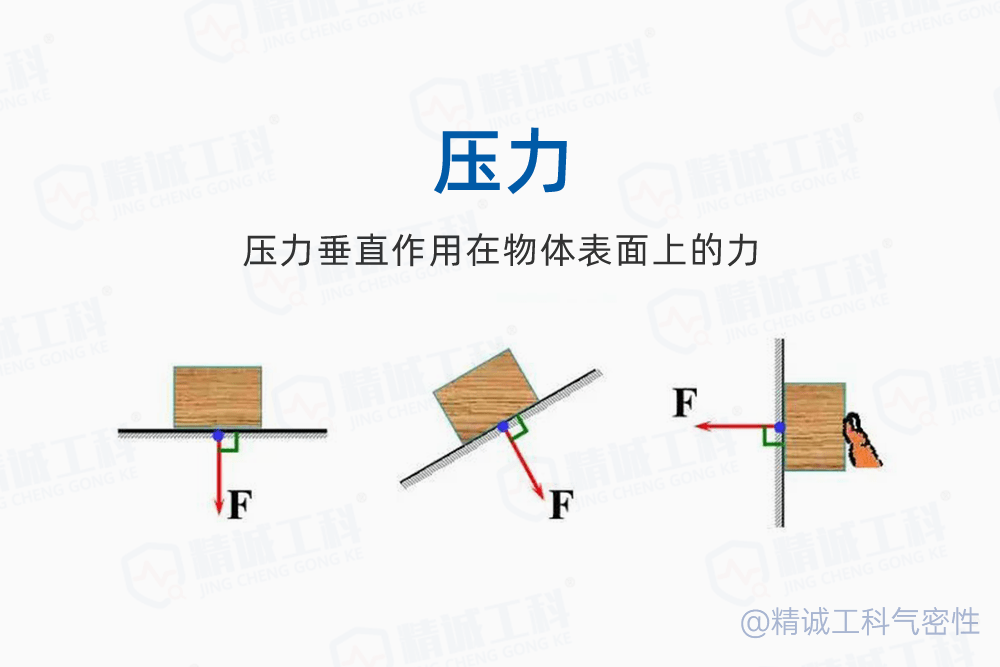
2. Units of pressure
The variety of units of pressure reflects its wide range of applications in different fields:
• 帕斯卡(Pa):国际单位制(SI)中的压力标准单位,每 m²(平方米)面积上 1N(牛顿)力的压力,即 1Pa 等于 1N/m²
• 千帕(kPa):1kPa 等于 1000Pa,常用于工业测量
- Megapascal (MPa): 1 MPa equals 1000kPa, or 1,000,000Pa, commonly used in industrial measurements.
• 巴(bar):1bar 等于 100000Pa,常用于工程领域
- psi (pounds per square inch): 1 psi equals approximately 6894.76 Pa, primarily used in British and American systems.
• 标准大气压(atm):等于 101325 Pa,常用于气象学
...
II. Gauge pressure
1. Definition of gauge pressure
Gauge pressure, as the name implies, isPressure measurement relative to local atmospheric pressure.It tells us how much the measured pressure is above or below the surrounding air pressure (usually atmospheric).
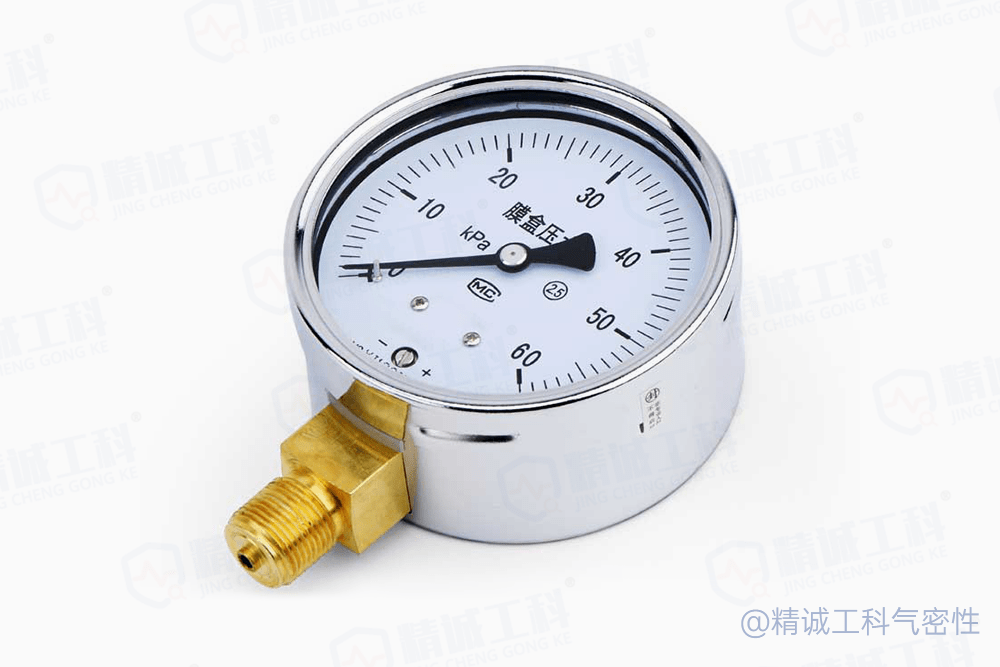
2. Principle of operation of gauge pressure
Gauge pressure measurements determine the amount of pressure by comparing it to atmospheric pressure.If the gauge pressure is positive, it means that the pressure is above atmospheric pressure; if it is negative, it means that the pressure is below atmospheric pressure.
III. Absolute pressure
1. Definition of absolute pressure
Absolute pressure isPressure measurement relative to a complete vacuum.It directly reflects the absolute value of pressure and includes all pressures including atmospheric pressure.
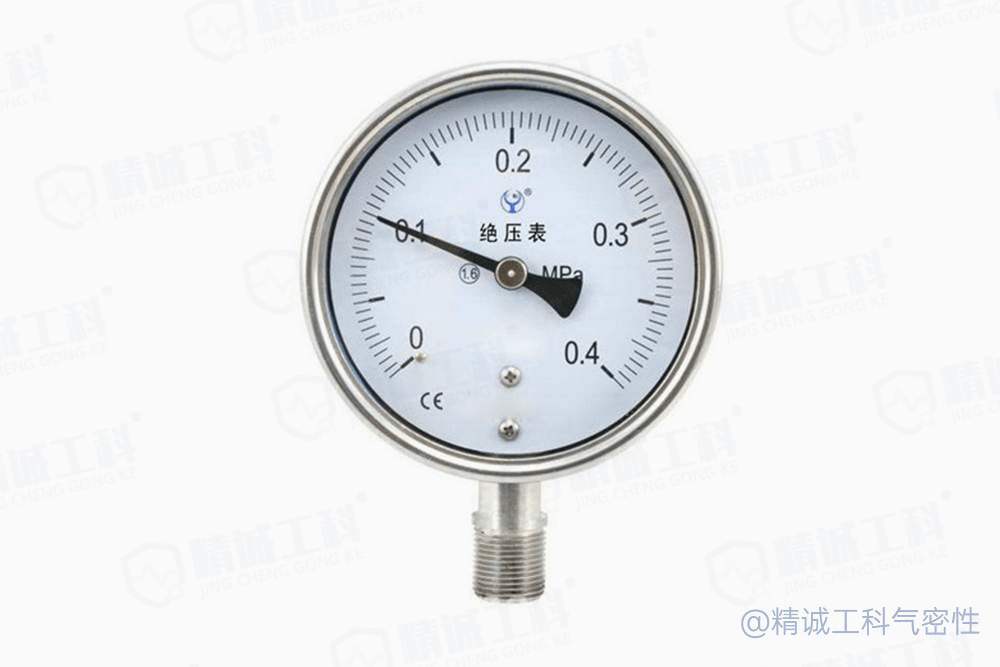
2. Principle of operation of the absolute pressure
Adiabatic pressure measurements ignore atmospheric pressure and focus on the pressure exerted by the object itself.
IV. Comparison of gauge pressure and absolute pressure
1. Differences in measurement principles
The main difference between gauge pressure and absolute pressure is the difference in reference pressure.Gauge pressure is measured relative to atmospheric pressure, while absolute pressure is relative to a complete vacuum.This leads to differences in application and interpretation between the two.
2. Conversion relationships
Conversion from gauge to absolute pressure requires consideration of the current atmospheric pressure value, which is usually accomplished by adding or subtracting a standard atmospheric pressure value with the following conversion formula:
- Absolute pressure = gauge pressure + atmospheric pressure
- Gauge pressure = Absolute pressure - Atmospheric pressure
V. Pressure measurement techniques
1. Types of pressure sensors
Pressure sensors include mechanical, resistive, piezoelectric, and many other types, each with its own specific operating principle and application scenarios.
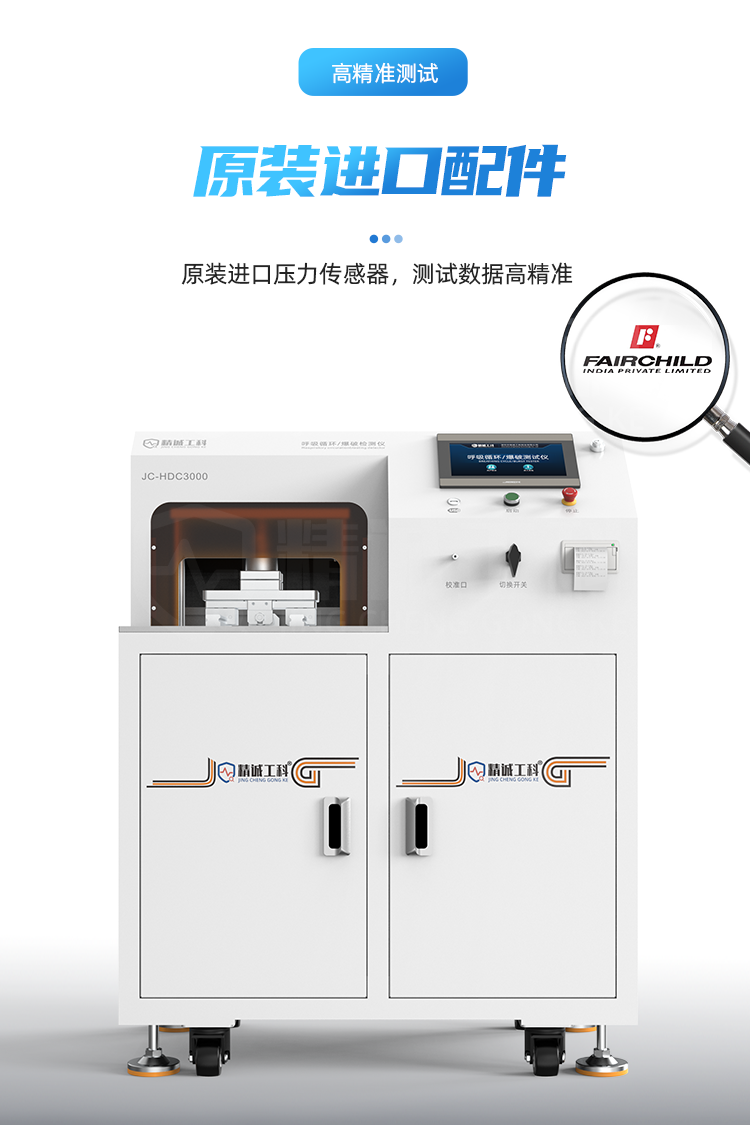
2. Accuracy of pressure measurement
Factors affecting the accuracy of pressure measurements include temperature variations, sensor accuracy, environmental conditions, etc., which need to be considered and controlled in design and use.
3. Calibration of pressure measurement
Regular calibration of pressure measurement equipment is an important step in ensuring its accuracy and reliability, especially in precision manufacturing and safety-critical applications.
VI. Pressure Measurement in Manufacturing
1. Quality control
Pressure measurement serves as a "quality inspector" in product quality control:
- Mold pressure control in injection molding to ensure accurate product dimensions
- Seal testing in food packaging to ensure food freshness
Food Box Sealing Test
2. Process monitoring
Pressure measurement acts as a "supervisor" during the production process:
- Pressure monitoring of chemical reactors to ensure safe reactions
- Pressure control of fluid transportation piping to prevent "running, bubbling, dripping and leaking".
3. Safety standards
Pressure measurement plays a "guardian" role in ensuring the safety of equipment and the working environment:
- Safety monitoring of boilers and pressure vessels to prevent "pressure burst"
- Pressure control of industrial gas storage tanks to avoid accidents
VII. Gas tightness test in relation to gauge pressure
1. Importance of airtightness testing
Airtightness testing is the process of evaluating a product or equipment for leaks or defects by measuring whether it can remain stable under pressure to ensure that the product does not suffer from quality problems.
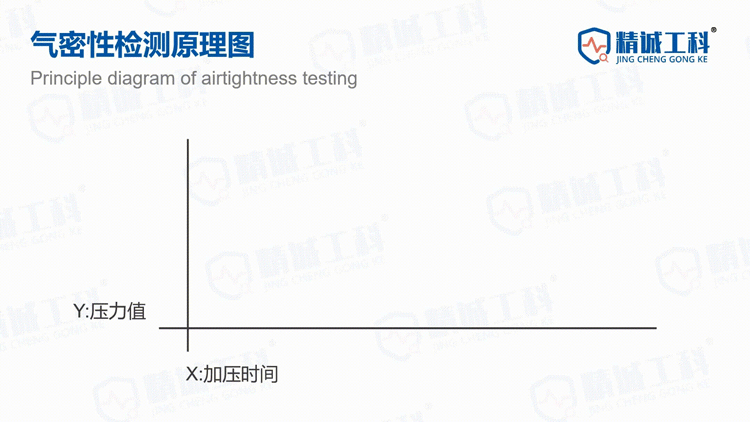
2. Gauge pressure in airtightness testing
表压传感器常用于Air tightness testing equipment中,通过测量产品部件内外压力差来判断是否存在泄漏或缺陷。它在汽车配件、消费电子、食品包装和医疗器械等行业中扮演着关键角色,保证产品质量和安全。
3. Advantages of airtightness testing
Gauge pressure measurements offer significant advantages in gas tightness testing:
- Highly accurate: detects small leaks
- Rapid response: real-time display of results
- Repeatability: suitable for batch testing
- Non-destructive testing: no damage to the object under test
By combining gauge pressure measurements and airtightness testing, the manufacturing industry is able to more effectively assure product quality and improve productivity while ensuring safety standards are met.
Summarize
Through an in-depth discussion of gauge pressure, absolute pressure and their applications in gas tightness testing, we not only deepen our understanding of the principles of pressure measurement, but also demonstrate its importance in modern manufacturing. Accurate pressure measurement not only improves productivity, but is also the 'guardian' of industrial safety and product quality.Let's look forward to the bright future of pressure measurement technology and witness the quality revolution of China's manufacturing industry together!
Welcome to contact JCGK to learn more about the domestic气密性检测仪的信息。让我们携手共创制造业的美好未来!