In daily life use, many products to face a variety of liquids, gases, dust attack, to ensure long-term normal operation, waterproof and dustproof essential.In order to ensure that the sealing and waterproof performance of the product meets the expected requirements(math.) genusCommon Test Methodsincluding throughstress test,Vacuum testing,Water tightness testcap (a poem)Spray Testetc.Their testing principles, methods, advantages and disadvantages are listed below:
Ⅰ.stress test
Generally refers to the positive pressure test or quantitative inflation test, also called gas test, testing instruments professional term:Airtightness Tester,Sealing Testeret al. (and other authors)
Principle:The product under test is enclosed in an airtight container, or the test area of the product under test is inflated by an auxiliary tooling fixture to observe whether leakage occurs. During the test, pressure changes can be monitored and recorded by various sensors and computer software and other equipment.
Methods:The product under test is placed into the workholding fixture chamber, the sealing device is closed and the test is carried out by increasing the internal pressure. Care should be taken not to over-increase the pressure during the test to avoid damage to the product.
Advantage:
- Tests can be performed in a short period of time with accurate and reliable results.
- Products can be tested for performance and tolerance in high stress environments.
- The testing process can be monitored and recorded by computer software and other equipment to facilitate data processing and analysis.
Drawbacks:
- It is not possible to test the performance of the product in a vacuum environment.
- Excessive increases in pressure during stress testing may cause damage to the product.
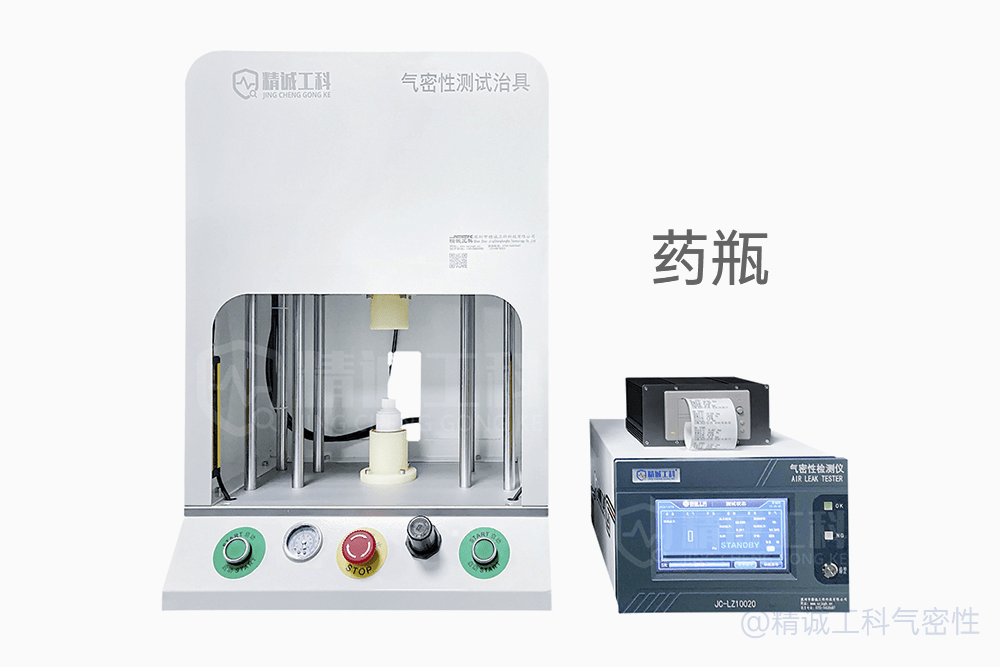
Ⅱ.Vacuum testing
Generally refers to the negative pressure test, also known as gas test, testing instruments professional term:Negative pressure air tightness tester,Helium Leak Detectoret al. (and other authors)
Principle:The product under test is enclosed in an airtight container, or the test area of the product under test is inflated by auxiliary tooling and fixtures to reduce the internal pressure and observe whether leakage will occur. During the test, pressure changes can be monitored and recorded by a variety of sensors and computer software and other equipment.
Methods:The product under test is placed into the fixture cavity, the seal is closed and the test is performed by reducing the internal pressure. Care should be taken not to over reduce the pressure during the test to avoid damage to the product.
Advantage:
- It is possible to test the performance and tolerance of products in a vacuum environment.
- The testing process can be monitored and recorded by computer software and other equipment to facilitate data processing and analysis.
Drawbacks:
- Unable to test product performance in high stress environments.
- Excessive pressure reduction during vacuum testing may cause damage to the product.
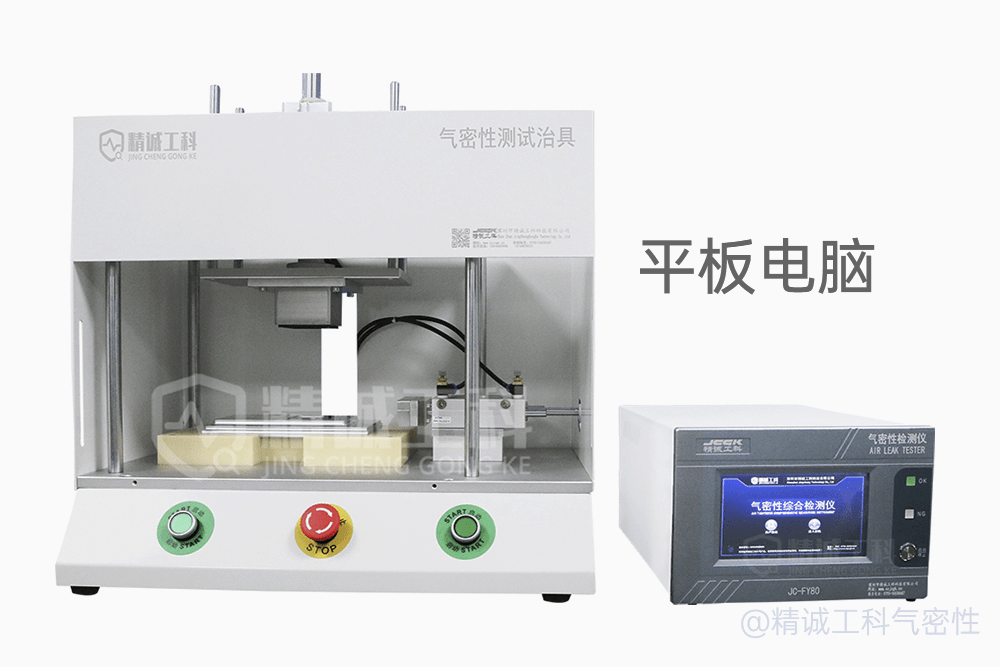
III.Water tightness test
Generally refers to the soak test, also called water test, testing instrument professional term:Water tightness tester,Water tightness testeret al. (and other authors)
Principle:The product being tested is enclosed in an airtight container filled with water or other liquid and observed for leakage. During the test, equipment such as various sensors and computer software can be used to monitor and record changes in the flow and pressure of the liquid.
Methods:The product under test is placed in an airtight container filled with water or other liquid, and the test is conducted by observing and recording changes in liquid flow and pressure. Care needs to be taken not to excessively increase the liquid pressure during the test to avoid damage to the product.
Advantage:
- Products can be tested for performance and tolerance in liquid environments.
- The testing process can be monitored and recorded by computer software and other equipment to facilitate data processing and analysis.
Drawbacks:
- It is not possible to test the performance of the product in a gaseous environment.
- Excessive increase in liquid pressure during water tightness testing may cause damage to the product.
Automotive filter element water tightness test
IV.Spray Test
Generally refers to the rain test, also known as water test, testing instruments professional term:Rainfall Tester, Spray Testeret al. (and other authors)
Principle:The product under test is placed in a device that simulates the environment in which it will be used, and water or other liquids are sprayed onto the surface of the product through a high-pressure nozzle to observe whether leakage or failure will occur. During the test, equipment such as various sensors and computer software can be used to monitor and record changes in the flow and pressure of the liquid.
Methods:The product under test is placed in a spray test device and tested by spraying water or other liquids. During the testing process, the time, intensity and direction of spraying need to be set according to the environment and conditions of the product. At the end of the test, the product surface needs to be checked for leakage or damage, and the corresponding data processing and analysis needs to be carried out.
Pros:
- The spray test can simulate the environment in actual use, and the test results are more realistic and reliable.
Drawbacks:
- It is not possible to test the performance of the product in high pressure or vacuum environments.
- 喷淋测试过程中,如果喷淋的时间、强度和方向等参数设置不当可能会影响测试结果的准确性。
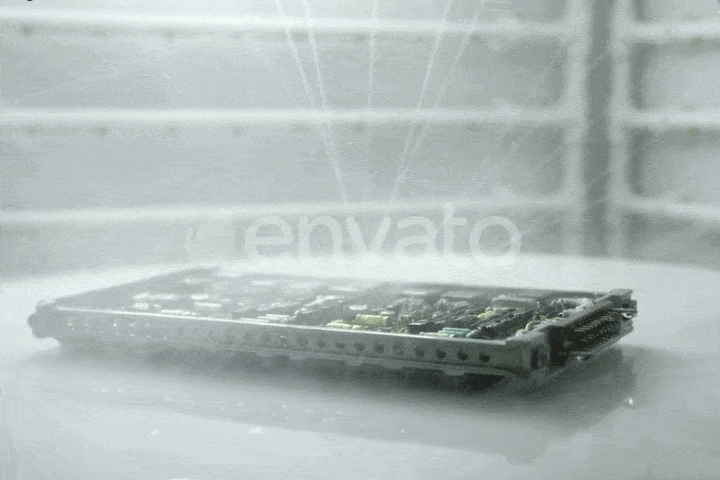
V. Summary
以上四种测试方法都有各自的优缺点,选择测试方法应该根据被测试物体的实际情况来进行选择。同时,为了确保测试结果的准确性,测试过程中需要注意测试设备的精准度和测试环境的控制,并结合其他测试方法进行综合测试,以确保产品的气密性防水性能符合相关的标准和要求。