I. Leakage rating of valves
Imagine a chemical plant where a tiny valve leak on a critical pipeline could cause millions in damage or even a safety incident. That's why valve leakage ratings have become the 'lifeline' of industry.
The leakage rating of the valve is an important indicator of how tightly the valve closes. Different application scenarios require different sealing performance of the valveIn addition, different standards for leakage ratings have been developed as a result. At present, the main international commonly used valve leakage level standards are as follows:
ANSI/FCI 70-2 (American Fluid Control Association Standard): This is one of the most widely used standards.The leakage classes of valves are categorized into six classes, Class I through Class VI, with Class VI having the lowest leakage and representing the most stringent sealing performance.In the case of the "Bubble Seal", it is often referred to as a "Bubble Level Seal" or "Zero Leakage" (in practice it is not absolute zero leakage, but a very small, acceptable amount of leakage).
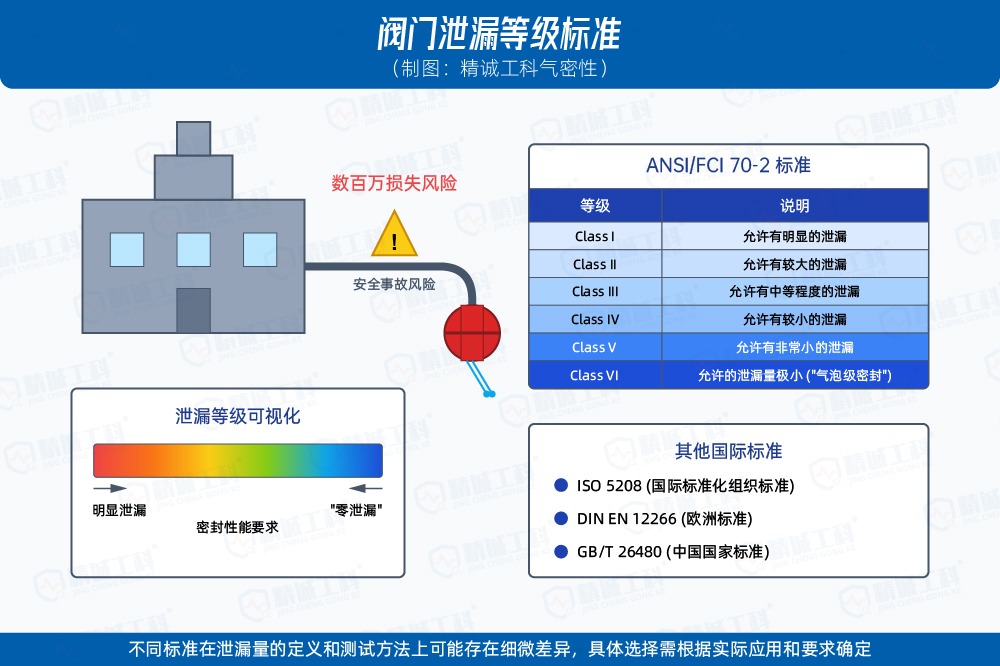
- Class I:Visible leaks are allowed and are not normally an acceptance criterion.
- Class II:A large leakage is allowed and is suitable for applications where sealing requirements are not high.
- Class III:Allows for moderate leakage and is suitable for general industrial applications.
- Class IV:Smaller leaks are allowed and are standard for many general purpose valves.
- Class V:Very small leakage is allowed for applications with high sealing requirements.
- Class VI:The permissible leakage is very small and is usually used where a tight seal is required, such as in certain gas or vacuum systems.
ISO 5208 (International Organization for Standardization standard): The standard also defines the pressure test of valves, which includes a leakage test. It specifies different leakage allowances depending on the type of valve and pressure class.
DIN EN 12266 (European Standard): The standard also provides for leakage testing of valves and defines different leakage classes.
GB/T 26480 (China National Standard): This standard is equivalent to ISO 5208, which specifies the shell test, sealing test, etc. for various types of industrial valves.
It should be noted that different standards may have slight differences in the definition of leakage and test methods, the specific choice of which standard needs to be determined according to the actual application and customer requirements.
Second, the valve airtightness testing principles and methods
The airtightness test of the valve is designed to verify the ability of the valve to prevent the medium (liquid or gas) from passing through the sealing surface under the closed state, and whether there is any leakage to the outside of the valve body and the permeable membrane and other parts of the valve.
Detection Principle:The basic principle of airtightness testing is to apply a certain pressure to the valve, and then detect the size of the valve leakage within a certain period of time. If the amount of leakage exceeds a preset standard, the valve is judged to be unqualified for airtightness.
Detection Methods:According to the detection of different parts and media, commonly used valve airtightness testing methods are mainly the following:
1. Seal test
Used to detect the leakage of medium through the sealing surface of the valve seat when the valve is closed.
Gas test: Usually air or nitrogen is used as the medium, a specified test pressure is applied to one side of the valve and leakage is detected on the other side. Detection methods include:
- Bubble method (water immersion or soap application): Immerse the valve in water or apply soap to the sealing area and observe whether bubbles are generated. This method is intuitive and simple, but not very accurate.
- Pressure drop method:After applying test pressure to the valve, the pressure drop is monitored for a certain period of time. The amount of leakage is determined by the size of the pressure drop. This method is highly accurate and can quantitatively analyze the leakage rate.
- Flowmeter method:A highly sensitive flow meter is connected to the leakage side of the valve to directly measure the flow of the leaking medium. This method provides direct access to leakage data.
Liquid test: Usually water is used as the medium in a manner similar to the gas test, but leakage is usually determined by observing the presence of liquid droplets dripping or forming a wet stain on the leakage side.
2. Shell test ((Strength test and air tightness test)
It is used to test whether leakage or rupture occurs when the valve shell, bonnet and other parts are subjected to a certain pressure. Usually, a test pressure higher than the working pressure is applied to the inside of the valve, and then the valve body and connection parts are observed for leakage.
The choice of test method needs to be determined by the type of valve, size, pressure rating, medium and required leakage level.
III. Jingcheng EngineeringAirtightness testing equipmenttestimonials
Shenzhen Jingcheng Industrial Technology has more than ten years of experience in the field of airtightness testing, we are committed to providing high precision, high efficiency, high stability for various industries.Air tightness testing equipmentand customized solutions. For airtightness testing of valves, we recommend the following types of instruments:
JC-TC Series Airtightness Tester (pressure decay method):
specificities: Adopting high-precision pressure sensors and advanced algorithms, it can quickly and accurately detect internal and external leakage of valves. Multiple test modes can be set to meet the requirements of different leakage levels. Support data storage and export, convenient for quality traceability. Special fixtures can be customized according to valve size and interface.
Method of application: Mainly used for seal testing and shell testing by the pressure decay method.
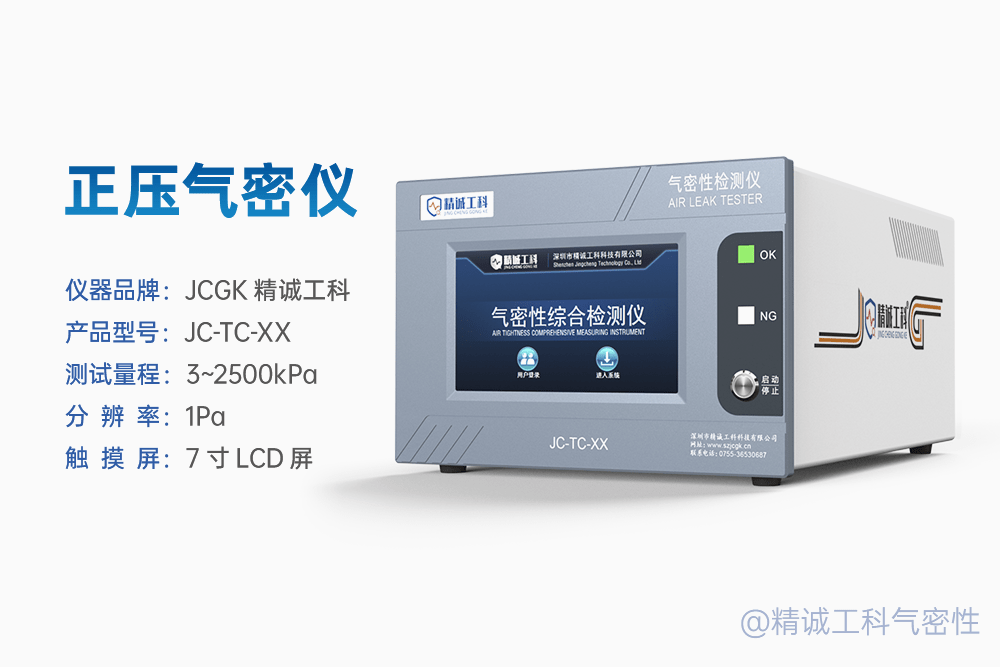
JC-FY80 Series Airtightness Tester (negative pressure vacuum method):
specificities: Suitable for valves that are pressure sensitive or require gas tightness testing under negative pressure conditions. Also characterized by high precision and high efficiency.
Method of application: Mainly used for sealing tests by the vacuum decay method.
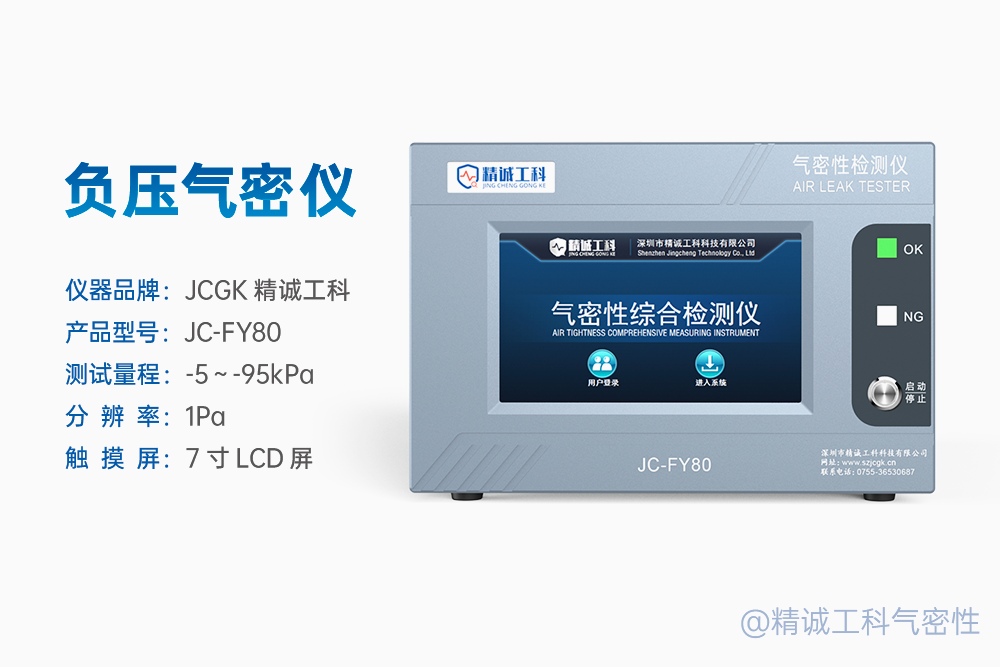
JC-LM5008 Series Gas Flow Detectors (flow method):
specificities: Equipped with a high sensitivity flow sensor, it can directly measure the leakage flow of the valve, and is suitable for applications where leakage is a clear requirement.
Method of application: Mainly used in the flowmeter method for sealing tests.
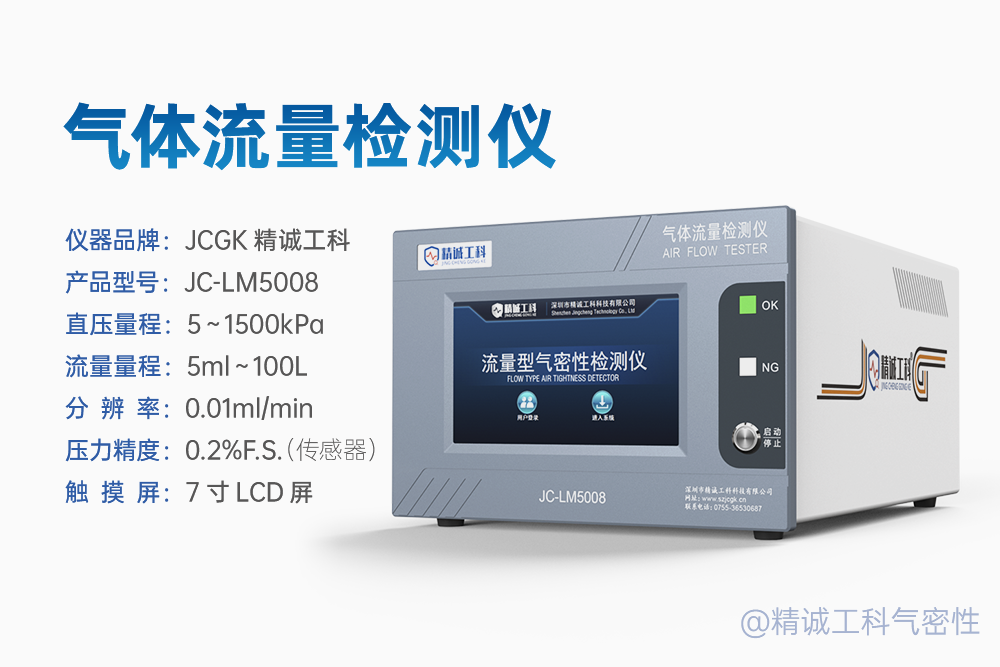
Customized airtightness testing system:
specificities: In response to the batch testing needs of valve manufacturers, thePrecision Engineering can provide automated and semi-automated customized airtightness inspection systems with integrated tooling fixtures, automatic loading and unloading mechanisms, data management systems, etc. to improve inspection efficiency and reduce labor costs.
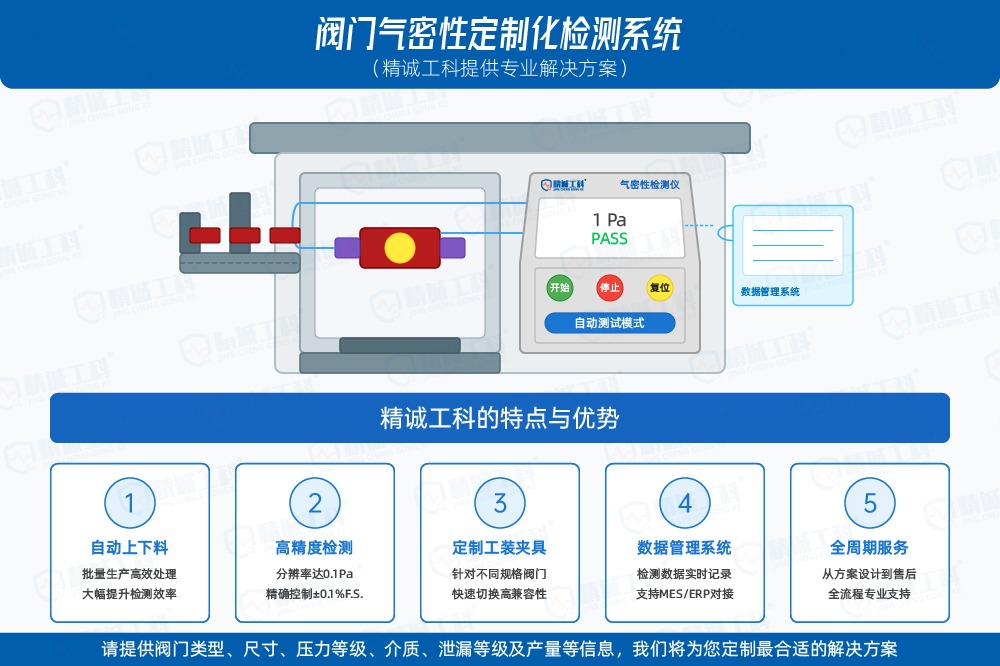
When selecting a specific instrument model, please be sure to provide details of your valve type, size, pressure rating, medium, required leakage rating, and throughput, and our professional engineers will recommend the most appropriate solution for you.
You can visitJingcheng Gongke airtight official websiteOr contact us directlyFor more detailed product information and technical support. We are committed to escort the quality of your valve products!
Original Statement: this paper was written byShenzhen Jingchenggongke Technology Co., Ltd.Written by the technical team, reproduced with attribution.Data sources:Precision Engineering internal test data and customer cases.