I. Importance of connector sealing test
Current connectors are an integral part of electronic equipment, and the sealing of their interfaces is directly related to the performance, reliability and safety of the equipment. Poor sealing can lead to:
- Electrical Failure: Moisture, dust or other contaminants inside the connector can lead to short circuits, poor contact, corrosion and other problems, affecting the normal operation of the equipment.
- Shortened equipment life: Long-term exposure to harsh environments and poorly sealed connectors are more likely to be damaged, shortening the use 2. life of the equipment.
- Safety hazards: In certain high-pressure or special application scenarios, poor sealing of connectors may even lead to safety accidents.
Therefore, it is critical to perform rigorous sealing tests on current connectors.
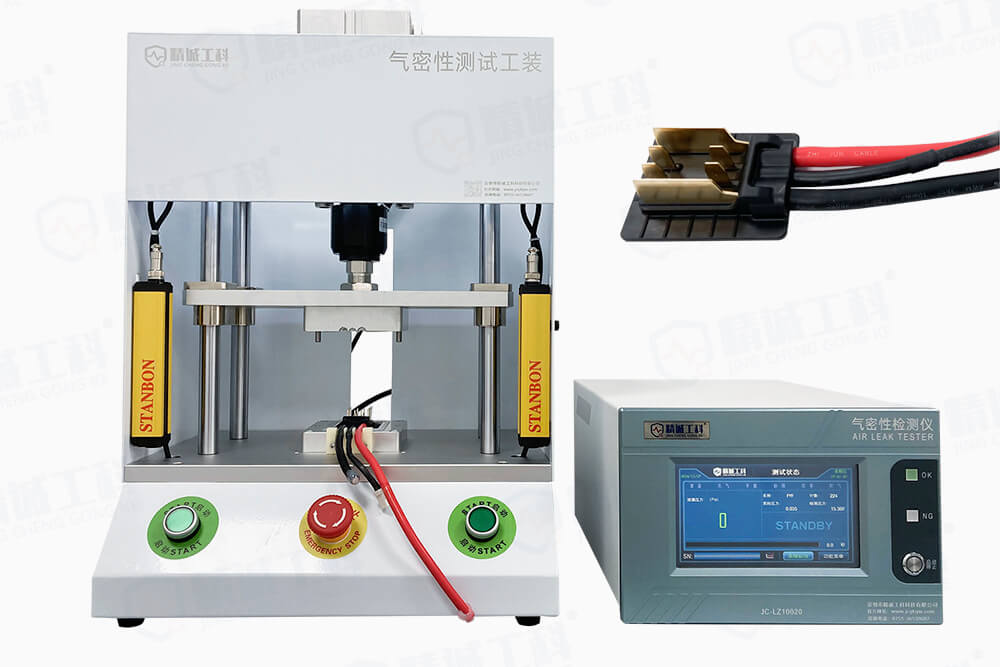
Ⅱ.Commonly used airtightness testing methods
Depending on the application scenario and sealing requirements, the following inspection methods can be used:
1. Air Tightness Test (Air Leak Test)
- Principle: utilizationAirtightness TesterA gas (e.g., dry air, nitrogen) at a certain pressure is filled inside the connector, and the sealing performance is evaluated by detecting the pressure change (pressure drop method).
- Advantage: High sensitivity for detecting small leaks; relatively simple and fast testing process; quantitative analysis possible.
- Applications: Widely used in automotive, aerospace, medical equipment, communications and other fields, especially for products with high sealing requirements.
- Precision Industrial Solutions: Precision Engineering provides high-precision and high-stabilityAirtightness TesterIt can meet a variety of demanding test requirements and provide customized test solutions.
2. Immersion Test
- Principle: Submerge the connector in water and observe if bubbles come out or water enters the inside of the connector.
- Criteria: International standards such as IEC 60529 (IP protection class), SAE J2030, etc. are usually followed.
- Advantage: Intuitive and easy to understand.
- Limitations: Can only detect larger leaks, cannot quantify leakage and may cause damage to some electronic connectors. Mainly used to verify the waterproof rating of a product.
3. Tracer Gas Method (TGM)
- Principle: A tracer gas such as helium is used to fill the inside of the connector, and the leakage of the tracer gas is detected by a leak detector.
- Advantage: Extremely sensitive to detect small leaks.
- Limitations: Relatively high cost and requires specialized equipment and operators.
III.Choosing the right sealing test method
The choice of inspection method depends on the specific application scenario and sealing requirements of the connector. Example:
- Automotive connectors: A combination of airtightness testing and water immersion testing is often used to ensure reliable operation in a variety of harsh environments.
- Underwater connectors: A more rigorous immersion test or even a high-pressure watertightness test is required.
- Precision instrument connectors: Gas tightness testing or tracer gas methods are often used to ensure that they work reliably in a variety of environments.
IV. Professional solutions from Precision Engineering
With more than 10 years of experience in the industry, Precision Engineering offers customized leak test solutions and high-qualityAir tightness testing equipment, included:
differentAirtightness Tester::
Covering a variety of testing principles such as differential pressure comparison method, gas flow method, volumetric quantitative method, helium mass spectrometry leak detection method, positive or negative pressure method, etc., to meet the testing needs of different products.
Customized tooling and fixtures:
Specialized tooling and fixtures are designed and manufactured according to the shape and size of the connector to ensure testing accuracy and efficiency.
Professional after-sales service and technical support:
Provide comprehensive after-sales service and technical support to ensure that customers get the best experience in the process of use.
Summarize
By using the correct sealing test method, you can effectively improve the quality and reliability of connector products, reduce the loss caused by leakage, and enhance market competitiveness. Precision Industrial Technology is committed to providing customers with the most professional airtightness testing solutions for your product quality protection.