In industrial production and daily life, many products need to have good sealing performance to prevent gas or liquid leakage, so as to ensure the normal operation and service life of the product.
For example, car tires need good seals to maintain air pressure, food packaging needs good seals to prevent spoilage, and medical devices need good seals to ensure sterility.Sealability testing is an important means of evaluating the sealing performance of a product.
Imagine, if the sealing of diving equipment is not good, water will penetrate into the interior, resulting in damage to the equipment and even endangering the lives of divers. This fully illustrates the importance of sealing testing.
I. Analysis of concepts related to sealing test
- Sealing Performance: Refers to the ability of a product or equipment to prevent gas or liquid leakage in a closed state. Sealability is one of the important indicators of product quality.
- Leakage: It refers to the phenomenon of gas or liquid leakage through tiny pores or gaps in products or equipment. Leakage can lead to degradation of product performance, waste of resources, and even safety accidents.
- Leakage Rate: Refers to the amount of gas or liquid that passes through a leakage channel per unit of time. Leak rate is an important indicator of the extent of leakage.
- Sealing Test (Sealing Test) / Leak Test / Air Tightness Test Refers to the test process of detecting whether the product or equipment can effectively stop gas or liquid leakage under closed condition through specific methods and equipment.
- Leak Detection Equipment (LDE): Refers to specialized equipment used to perform leakage testing, such as Air Leak Tester, True Water Tester, etc.
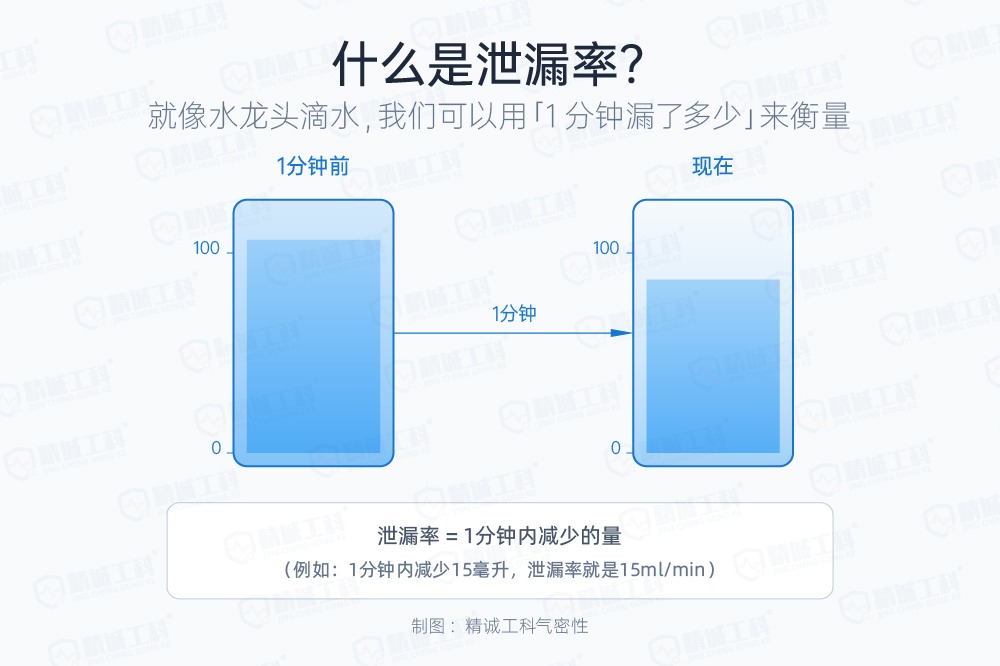
Second, commonly used sealing test methods
1. Immersion Test/Bubble Test
Immerse the product under test in water and observe for bubbles.
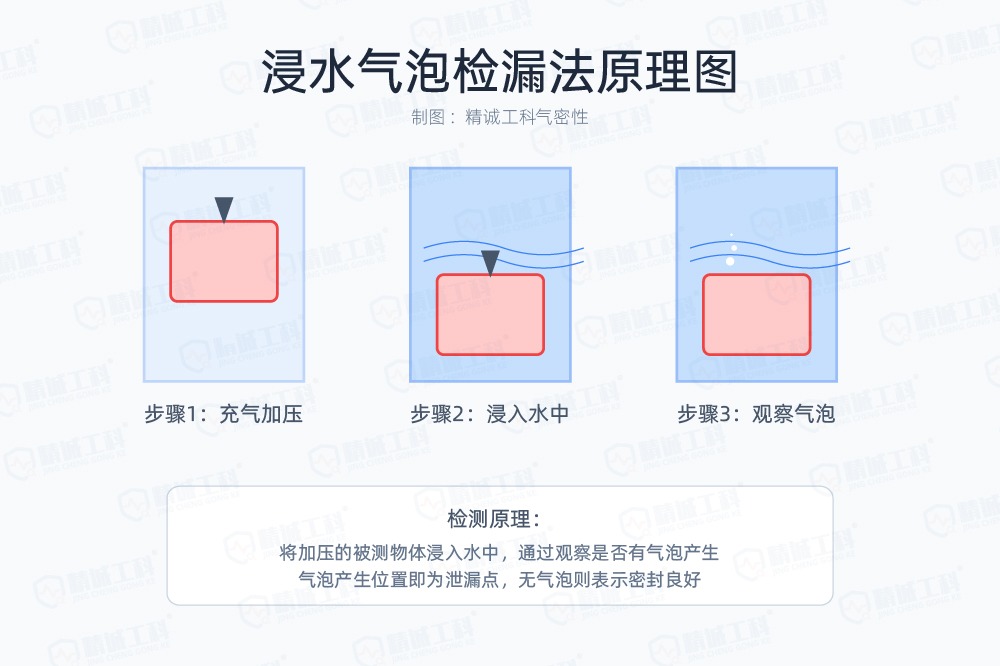
2. Pressure Decay Method (PDM)
Also known as the Pressure Drop Method, it determines whether a leak exists by monitoring the change in pressure inside the product under test over time.
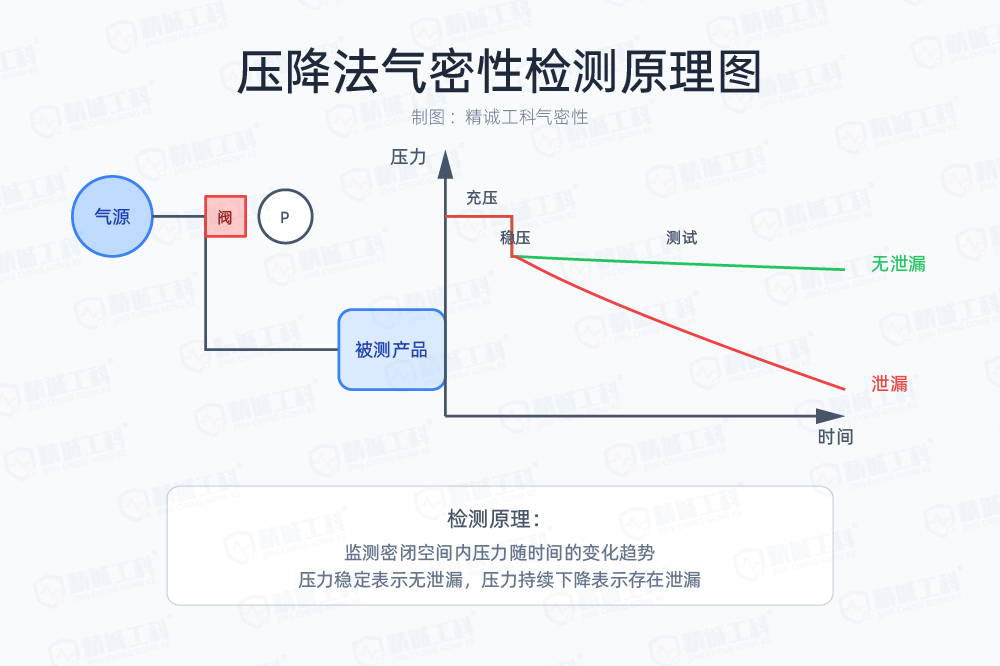
3. Differential Pressure Method (DPM)
Leakage is accurately determined by comparing the pressure difference between the standard and the product under test.
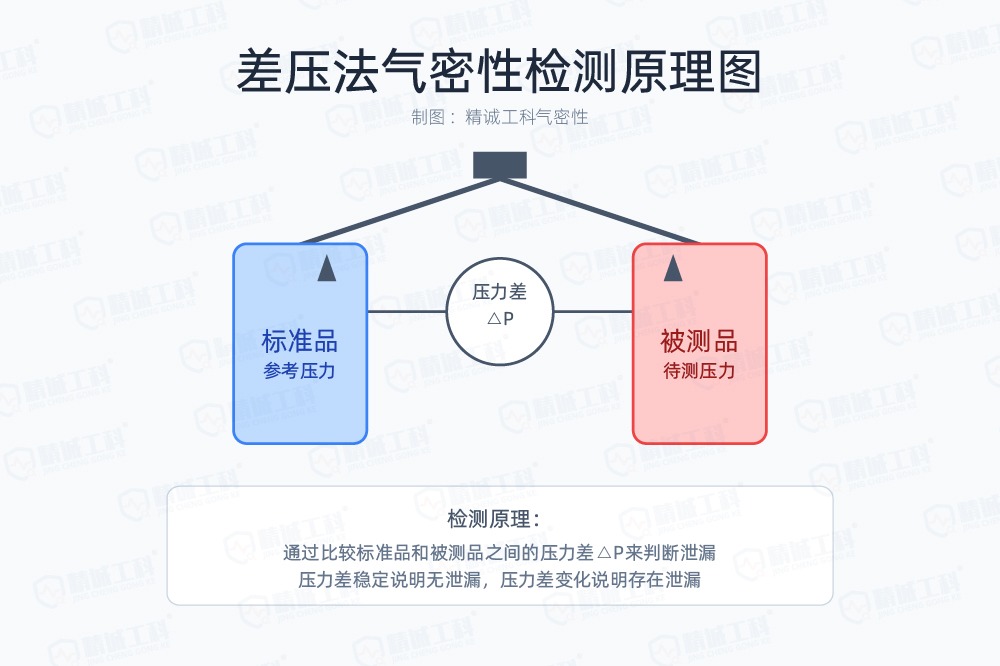
4. Tracer Gas Method (TGM)
Also known as Helium Detection, this method uses a tracer gas such as helium to detect leaks and accurately measures the amount of leakage by detecting the concentration of helium ions with a high degree of sensitivity.
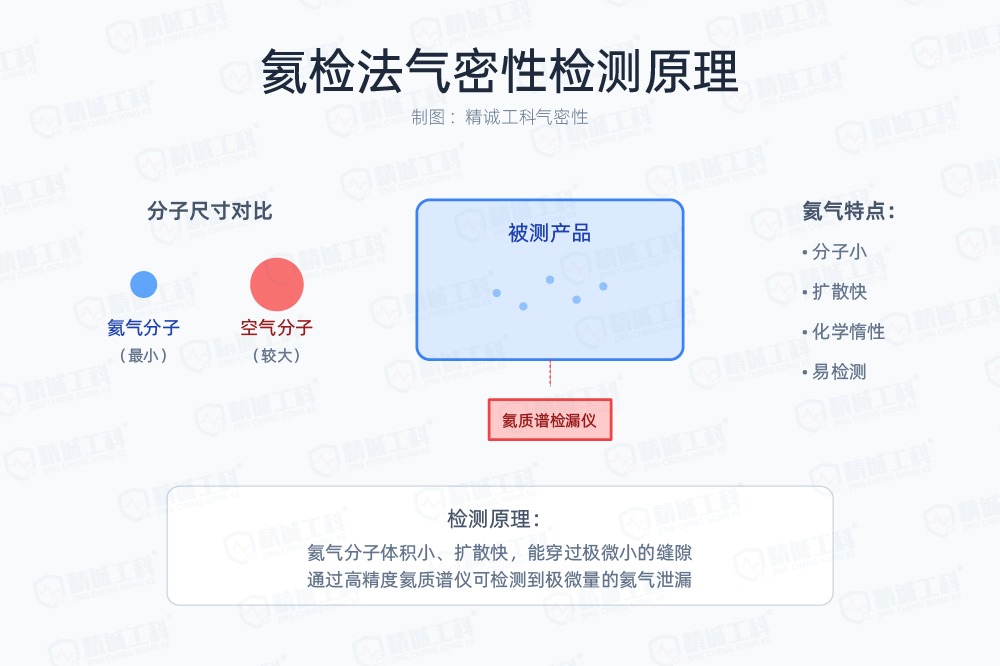
III.Sealing test equipmentselection
Airtightness Tester(Air Leak Tester):
It is an instrument specially used for testing the air tightness of products or equipment. It usually adopts the pressure drop method, differential pressure method or helium detection method for testing, which has the advantages of high precision and simple operation.
Die casting differential pressure air tightness test case
True Water Tester(True Water Tester):
An instrument for detecting liquid or gas leaks. It can detect the location and size of leaks and help users find and solve leaks in time.
Medical 3-way valve air tightness + real water test case
Fourth, Jingcheng Industrial Technology: professional sealing test solution provider
Conducting effective sealing tests can help companies improve product quality, reduce losses due to leakage, and enhance market competitiveness.
With more than 10 years of industry experience, Precision Engineering Gas Tightness can provide you with customized leak test solutions and high-quality testing equipment, includingAirtightness Tester,Waterproof Tester,Burst Tester,Leak test equipment,Respiratory Cycle Testeretc.
We are committed to providing solutions comparable to imported quality at domestic prices to help you reduce costs and improve efficiency.
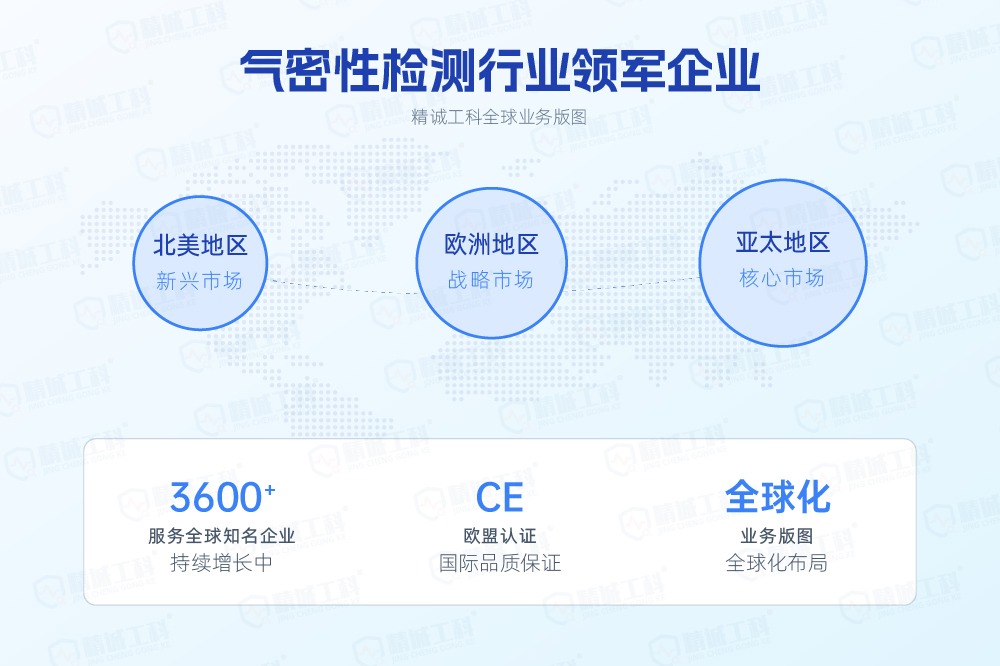
After years of development and accumulationPrecision Engineering has become a well-known domestic and internationalLeak Detector Brandsand supplier of fully automated airtightness testing solutionsWith more than 3,600 customers in Asia Pacific, Europe and North America, our products are CE certified to better serve the international market.
Choose Precision Engineering to protect your product quality from potential risks. To learn more about leak testing, please visit our website or feel free to contact us.