I. Principle of integrated die casting
Die casting is a metal product usually made of metal materials such as aluminum, copper and zinc. Integral die castings are manufactured in a single process through die casting technology with a high degree of precision and complexity. In integrated die casting, metal materials are injected into a mold at high temperature and pressure and cooled and solidified in a short period of time to form a complete casting.
Due to the efficiency and precision of the integrated die casting process, these castings typically have excellent mechanical properties, surface finish, and density, and can be fabricated into very complex shapes that are inindustrial manufacturing,Auto Parts,electronic productIt is widely used in such fields as.
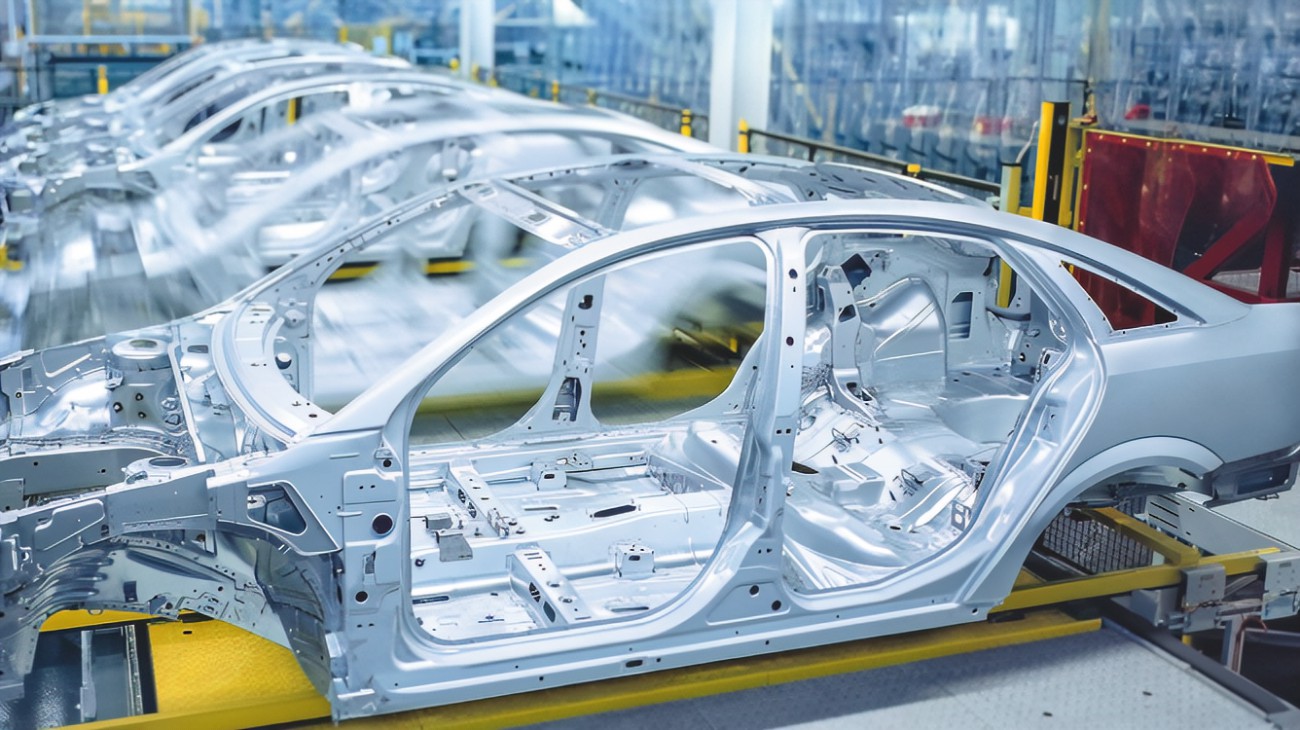
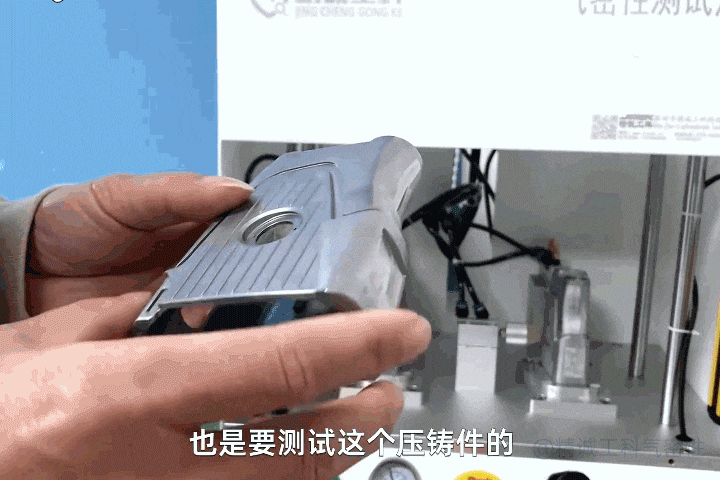
Airtightness testing of integrated die castings is usually performed using two methods, as follows::
Second, the soaking water method
Apply soapy water to the surface of the casting workpiece and observe whether bubbles are generated. This method of testing efficiency is not high, human factors have a greater impact on the leakage test results, there is no accuracy to speak of, the data can not be quantified, it is not convenient to track and cause judgment.
The disadvantages are secondary contamination of the product, the need for drying and wiping, and high labor costs. The only advantage is that leaks can be foundIn many cases, very small air bubbles are not easily detectable by the naked eye.
III. Pressure drop method
In airtightness testing of integrated die castings, the pressure drop method is often used (Air tightness tester) to test whether the casting has good airtightness. The method is to put the tested casting into a closed cavity and inject a certain pressure into the cavity, and then determine whether the casting is airtight or not by observing the pressure change in the cavity.
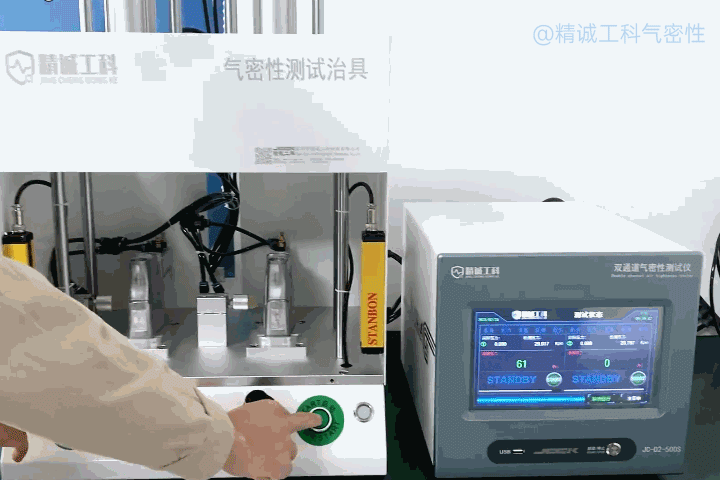
The disadvantage is the relatively high cost of the instrument, which is momentarily difficult for many MSMEs to accept.Benefits include high inspection efficiency and labor savingsThe existence of the reference material minimizes the impact of the test on the external environment and the differences in the work itself, overcomes the shortcomings of the soaking method, and improves the efficiency, accuracy and reliability of the test.
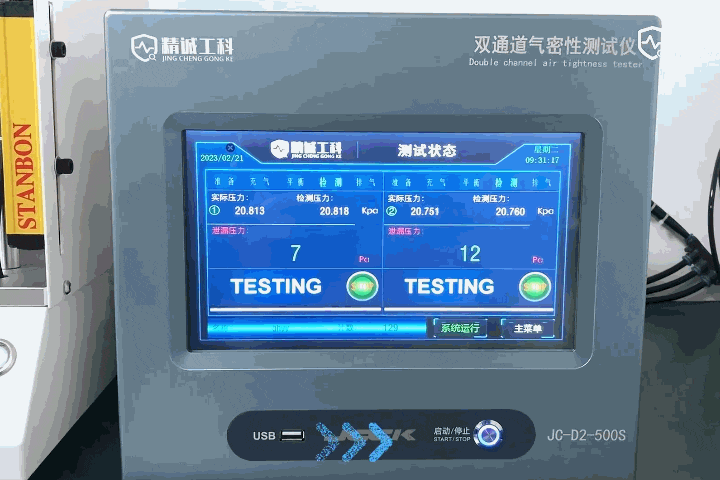
Fourth, air tightness testing precautions
The following points also need to be taken into account when performing airtightness testing of integrated die castings:
- Air tightness testing equipmentThe precision and accuracy should be in accordance with the relevant standard requirements.
- The surface of the die casting should be cleaned before testing to ensure that the surface is free of impurities and oil, etc.
- Care should be taken to avoid heat and stress on the casting during testing to avoid affecting the test results.
V. Summary
The airtightness test of integrated die castings can be done by methods such as soaking method and pressure drop method, but attention needs to be paid to the followingAir tightness testing equipmentaccuracy and precision, as well as the cleanliness of the casting surface and the avoidance of heat and force during the inspection process.
telescopesAir tightness testing equipmentTests shell castings for air and water leakage.
Shenzhen Jingcheng Engineering as a focus on airtightness testing more than 10 years of equipment manufacturers, has always been committed to China's smart manufacturing, to support the waterproofing products in various industriesAir tightness testerCustomized and fully automatedAirtightness testing programSupply.